一位老師傅根據多年工作經驗,總結了CNC加工中心加工模具零件應注意的問題。
1 基準及輔助基準的選擇、加工、標識
如果說圖紙是工程的語言,那么圖紙上的基準是加工和裝配的路標,加工中心在加工零件時,首先必須在圖紙上尋找基準,在通常狀況下,零件須經過刨床加工、磨床加工2面后,才能進入CNC加工的。在確定基準時,通常狀態下,零件上只要銑出一條基準邊和一個基準孔或一個銷孔或導柱孔,并在圖紙上標識。操作工也可以在工件上做記號,以便于下一次返工,測量尺寸時做基準。然而對于復雜的三維曲面,通常都需要進行五面三維加工。底面進行銷孔、鍵槽、螺絲孔的加工,所以我們引入輔助基準的概念。例如,要設計加工一個直徑為600mm的半球零件,半球要進行三維曲面加工,半球底面要加工鍵槽定位或用銷孔定位及螺絲孔,如圖1、圖2所示,所以,在設計時,一定要另外多設計4個工藝柱子,加工時,4個工藝柱子與底面互為基準進行加工,然后再加工一塊工裝板,在工裝板上加工一個基準邊和一個基準孔(X800,Y0),同時在工裝板上加工出相應的定位銷孔和螺絲孔,這樣才能把鑄件鎖在工裝板上,就可以進行三維曲面加工了。該工裝板的基準邊,基準孔,應在圖紙上標識,存檔,當然。工裝板也可以用下模板代替。
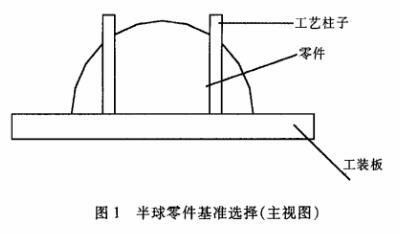
對于復雜曲面的零件來說,一個工位狀態下進行三維加工是不能滿足要求的,可能要進行3個工位,甚至6個工位才能完成三維加工。例如,加工摩托車油箱內殼拉伸模的凸模時,要用3個工位才能完成三維的加工。由于該零件尺寸長660mm,寬330mm,高320mm,如圖3、圖4、圖5所示。這在一種工位上加工到位是不可能完成的,故需要加工一塊工裝板,在工裝板上加工一個基準邊和一個基準孔并加工與凸模上的螺絲孔、鍵槽或銷孔相對應的孔,在圖紙上進行標識,記錄下基準孔的坐標,這樣再進行A面(頂面)的三維加工,A面加工完后,在A面加工工位上銑出輔助基準E和H的尺寸并記錄在圖紙上,作為加工B面、C面時的對刀依據。在加工B面或C面時,必須先將角鐵爬表看正并裝夾在工作臺上,將工件翻轉90°,安裝在角鐵上。進行爬表,看正,校對X ,Y,Z的參考點,并把參考點基準轉到固定物上,同時操作員要記錄下來,以便讓下一班操作人員知道加工基準,并進行校對。這樣就能夠防止交接班出現錯誤,提高生產率。
2 粗加工的程序編制應注意的幾個問題
(1)編程人員在編程時應首先測量毛坯尺寸,使得定義毛坯尺寸與實物尺寸一樣.這樣就可以避免撞刀
(2)在編制挖槽層切粗加工程序時用,采用螺旋下刀,每層切深0.8-1.0mm,若不用螺旋下刀(受空間限制),直接下刀要用2個進給速度,即Z軸進給150mm/min和X,Y進給1500-2000mm/min。如果用一個進給速度,很容易產生打刀。
(3)在編制挖凹槽粗加工程序時應注意:①安全高度的選擇要正確,否則會產生打刀現象;②斜面很陡時,圓刀片接觸面積較大,容易產生震動及嗓音,這時主軸轉速要降低,每層切削深度約0.6mm左右,進給速度要相應變小。
(4)加工凸模,挖槽粗加工時,同時存在順銑與逆銑.這樣當深度銑到較深時,或加工到斜面坡度較大時,若逆銑聲音較大.震動較大,在這不良加工狀態下,建議停止加工,改變加工工藝,而采用等離外形加工,并限定深度進行單向順銑切削,這樣既好加工,又節省時間,延長刀具壽命,提高生產率。
(5)在編程切粗加工時,要注意選擇好刀具刀徑與間距的關系,程序編好后要進行實體模擬運行,檢查程序是否有過切現象,同時觀察每層層切是否加工到位,如果層切時刀間距太大,每層加工不干凈,產生多余的臺(柱)狀,這樣給下一刀層切加工帶來困難,甚至會發生打刀現象,需要重新計算直到完好為止。
3 精加工編程加工應注意的幾個問題
由于粗加工留下加工余量及受刀具的限制,粗加工大都采用PD40(R5mm)的刀具,精加工大部分用QT20、QT16、QT10等,局部小凹槽粗加工無法到位,留下余量較多,故在精加工之前,一定要先進行清根或半精加工,這樣使得余里*均勻,不會產生局部余量太多而產生打刀現象。
在編制等高外形的精加工程序的過程中,編程人員若采用直接下刀,則在下刀處會產生過切現象。這對于精密模具來講,是不可以的,故建議編程人員在編制等高外形的精加工時,一定要用進刀和退刀的方式導人,在定義下刀點時,在不重要的斜面上或在坡度較大的斜面下刀,這樣加工出來的表面質量較好。對于局部小凹槽而言,也可能上述刀具精加工曲面不能加工到位,故必須用*小的刀具來定義切削范圍,進行局部三維加工。
在編程加工中,若三維造型以凹模為準,則加工凹棋必須到位。加工凸模時,必須過切一個料厚,并在圖紙上或在程序上加以標識。這樣不會弄錯,否則很容易發生錯誤,加工出來沒有料厚,必須重新返工,影響模具交貨期,這種現象不能發生。